Most conventional robots are composed only of highly rigid elements such as high reduction ratio gears and metal housing parts, making it difficult for them to respond flexibly to contact with the external environment. As a solution to this problem, a mechanism called a series elastic actuator (SEA) with an elastic body between the reduction gear and the robot’s joint output shaft has been proposed. The SEA has two position sensors (or angle sensors) on the input and output sides of the elastic body, and the amount of elastic deformation can be measured from the difference of these values. The external force applied to the joint can be estimated by multiplying the amount of elastic deformation by a known elastic modulus (spring constant). This principle can be applied to both linear and rotational joints.
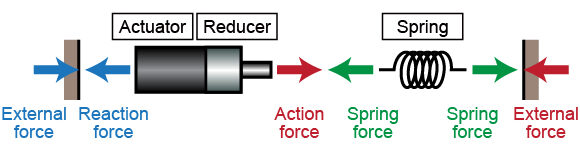
However, the elastic bodies generally used in these SEAs are metal springs, which tend to be specially shaped to achieve elastic properties in both forward and reverse directions of rotation, and require time-consuming cutting and quenching. In addition, since the amount of deformation within the elastic range of spring steel is small, the overall size of the spring tends to be large in order to achieve large deformation. In recent years, a series elastic actuator consisting of a rubber spring made of polymer material with symmetrical characteristics in both forward and reverse directions and supported in the shear direction has begun to be reported. Since the deformation and viscosity of rubber springs made of polymeric materials are larger than those of metal springs, they can be applied not only to torque sensors and series elastic actuators, but also to vibration suppression. In addition, by changing the size of the polymer material, the modulus of elasticity can be easily changed, allowing for greater design flexibility.
In this study, we focused on “polyurethane”, which has low viscosity among polymer materials, and measured its rotational elasticity and rotational viscosity when supported in shear direction for use in a robot joint. The measurements revealed that polyurethane with a diameter of Φ36 mm and a thickness of 10 mm exhibits high linearity in the range up to ±5 Nm, making it easy to estimate the torque.
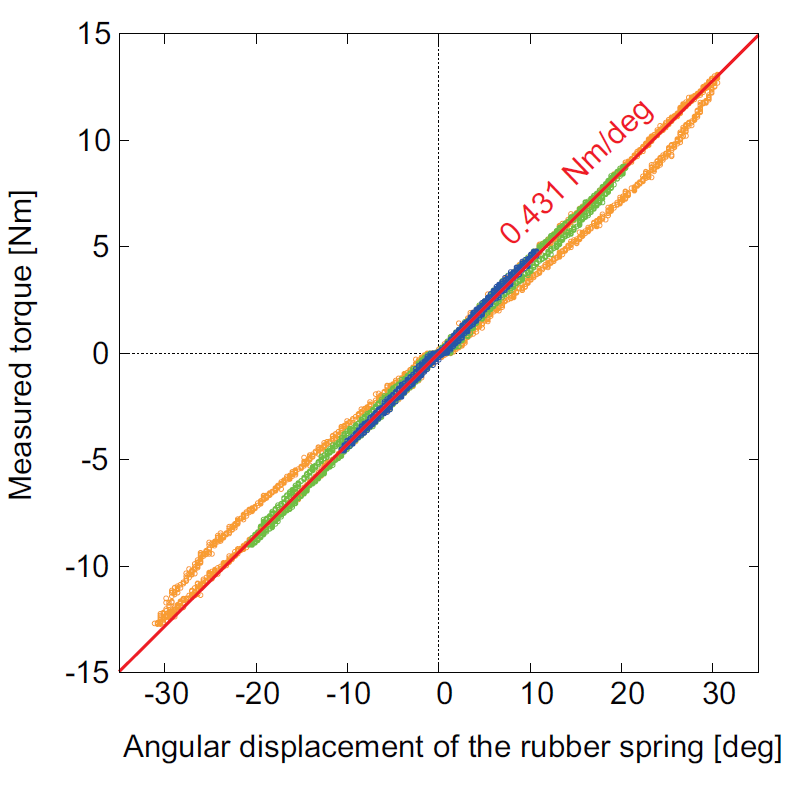
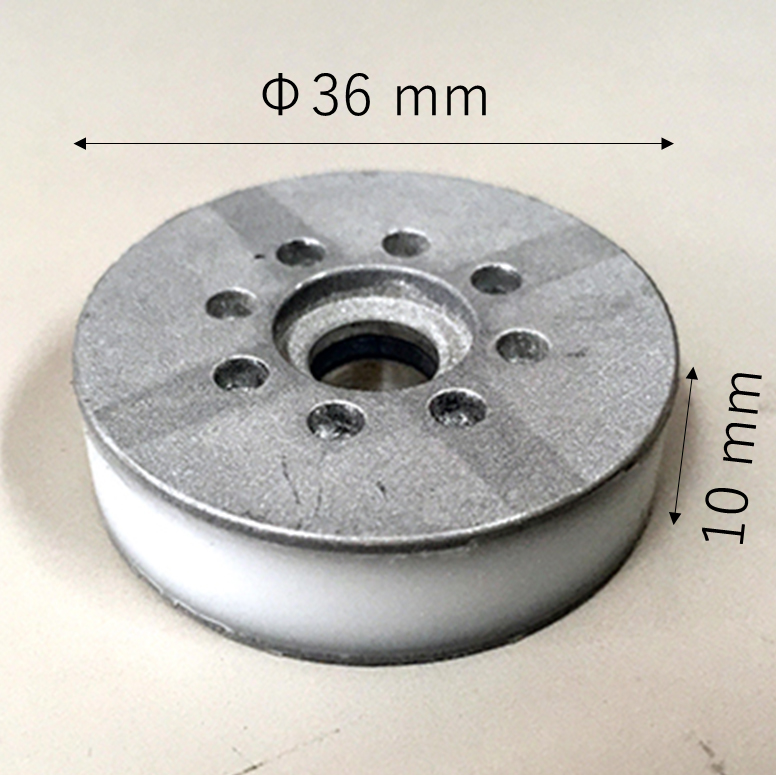
When ordinary polyurethane is fixed to metal parts, the adhesive surface tends to delaminate when force is applied, resulting in immediate rupture. To solve this problem, a high-strength series elastic actuator made of high-strength polymer material was fabricated using POLYMETAC (Mitsui Chemicals, Inc.), which intentionally corrodes metal surfaces by acid edging before fixing polyurethane. While a typical polyurethane actuator broke after about 10 Nm, the polyurethane used in this study improved durability to about 30 Nm for the same size actuator.
※本成果は,科学研究費助成事業(若手研究(B))「狭隘環境のための小型差動弾性アクチュエータの研究開発」17K14632の支援を受けました.
Related works
- Atsushi Kakogawa, Kenya Murata, and Shugen Ma, Automatic T-branch Travel of an Articulated Wheeled In-pipe Inspection Robot Using Joint Angle Response to Environmental Changes, IEEE Transactions on Industrial Electronics, Vo. 70, Iss. 7, pp. 7041-7050, 2023
- Atsushi Kakogawa, Kenya Murata, Shugen Ma, Vertical Bend and T-branch Travels of an Articulated Wheeled In-pipe Inspection Robot by Combining Its Joint Angle and Torque Controls, Proceedings of the IEEE/RSJ International Conference on Intelligent Robots and Systems (IROS 2022), pp. 13254-13259, 2022
- 村田憲哉,加古川篤,馬書根,1自由度能動関節のみを用いた連結車輪型管内移動ロボットのT字管走行 ―第2 報:角度センサの配置による関節角度およびトルクの計測性能の比較―,日本機械学会ロボティクス・メカトロニクス講演会 2022,2P1-M09,2022
- Atsushi Kakogawa, Yutaro Kushitani, and Shugen Ma, Automatic T-branch Travel of a Multi-link In-pipe Inspection Robot based on Joint Torque Value, 5th International Symposium on Swarm Behavior and Bio-Inspired Robotics (SWARM 2022), 2022
- Atsushi Kakogawa and Shugen Ma, A Multi-link In-pipe Inspection Robot Composed of Active and Passive Compliant Joints, Proceedings of the IEEE/RSJ International Conference on Intelligent Robots and Systems (IROS 2020), pp. 6472-6478, 2020
- 櫛谷侑太郎,加古川篤,馬書根,1自由度能動関節のみを用いた連結車輪型管内移動ロボットのT字管走行,日本機械学会ロボティクス・メカトロニクス講演会 2020,2P1-L08,2020
- 小川恭平,加古川篤,馬書根,川村貞夫,ロボット用せん断支持型高分子弾性要素の機械特性,日本機械学会ロボティクス・メカトロニクス講演会 2020,2P1-L07,2020
- Atsushi Kakogawa and Shugen Ma, An In-pipe Inspection Module with an Omnidirectional Bent-pipe Self-adaptation Mechanism using a Joint Torque Control, Proceedings of the IEEE/RSJ International Conference on Intelligent Robots and Systems (IROS 2019), pp. 4347-4352, 2019
- Atsushi Kakogawa and Shugen Ma, A Differential Elastic Joint for Multi-Linked Pipeline Inspection Robots, Proceedings of the IEEE/RSJ International Conference on Intelligent Robots and Systems (IROS 2018), pp. 949-954, 2018
Previous studies that served as references for this study
- G.A. Pratt and M.M. Williamson, Series Elastic Actuators, Proceedings 1995 IEEE/RSJ International Conference on Intelligent Robots and Systems. Human Robot Interaction and Cooperative Robots, pp. 399-406, 1995
- D. Rollinson, S. Ford, B. Brown, and H. Choset, Design and Modeling of a Series Elastic Element for Snake Robots, in Proc. the ASME Dynamic Systems and Control Conference, pp. 1-5, 2013
- D. Rollinson, Y. Bilgen, B. Brown, F. Enner, S. Ford, C. Layton, J. Rembisz, M. Schwerin, A. Willig, P. Velagapudi and H. Choset, Design and Architecture of a Series Elastic Snake Robot, in Proc. the IEEE/RSJ Int. Conf. Intelligent Robots and Systems, pp. 4630-4636, 2014