The maintenance of pipeline used for gas, water, sewage, and air conditioning is one of the major challenges facing mankind in urban society. In particular, it is difficult to inspect pipelines installed underground or in high-rise buildings from the outside. Therefore, identifying aging pipes is a costly and time-consuming task.
Commercial industrial endoscopes have been used for general pipe inspections. However, many pipes contain numerous bends and elbows and even T-junctions. A conventional push-on camera can only pass through two or three bends in such a path. For these reasons, there are high expectations for in-pipe inspection by a self-propelled robot that can pass through multiple bends and T-branches.
Our robot “AIRo” developed in this research consists of three joints, three omni-wheels for forward/backward motion, and two spherical wheels for roll rotation (rolling around the direction of travel). Since the axles and joint axes are on the same line, the AIRo can be significantly downsized without compromising functionality, and the range of adaptable inner diameters can be increased.
In the initial AIRo-1 and AIRo-2, all joints were designed to be passively bent by torsional coil springs, but in AIRo-5, a motor, reduction gear, and torque sensor are built into the central joint, enabling both angle control and torque control.
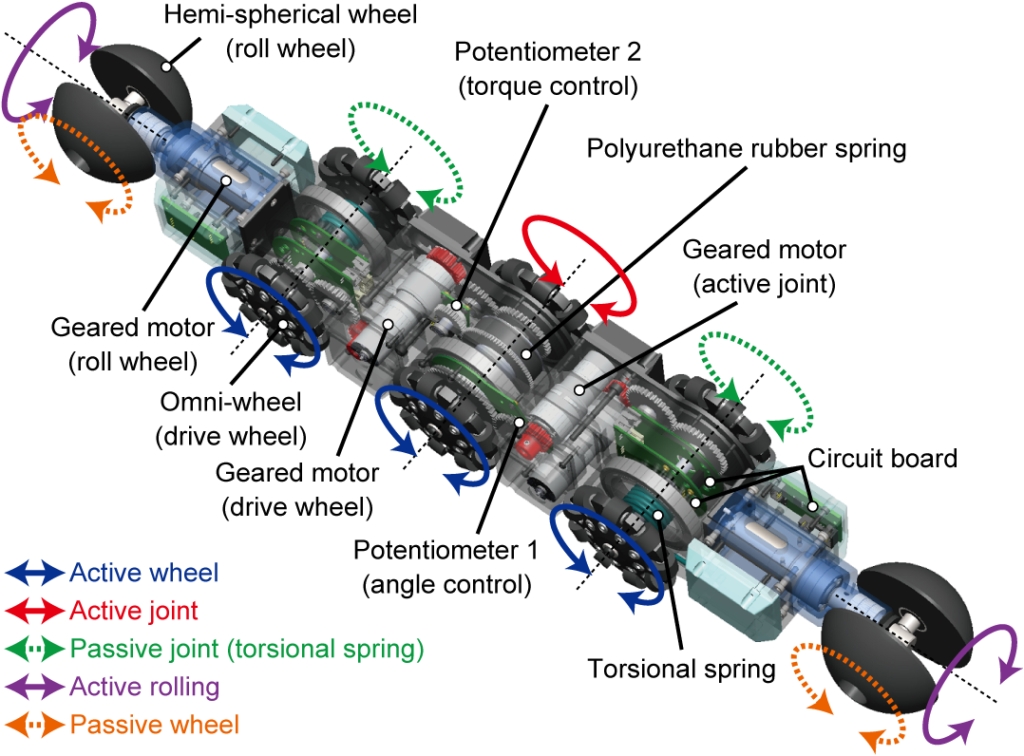
In AIRo-5.2, the latest model, passage through a bend is achieved only by joint torque control, while passage through a T-branch is achieved by switching between both joint angle and torque control. In particular, it was found that the T-branch can be successfully traversed by controlling the central joint angle with a cosine trajectory relative to the travel distance.
Since commercially available torque sensors are large and vulnerable to impact forces, our own developed polyurethane type series elastic actuator (commonly known as SEA) is mounted. This not only enables torque control in a limited space with an inner diameter of less than 100 mm, but also improves shock resistance.
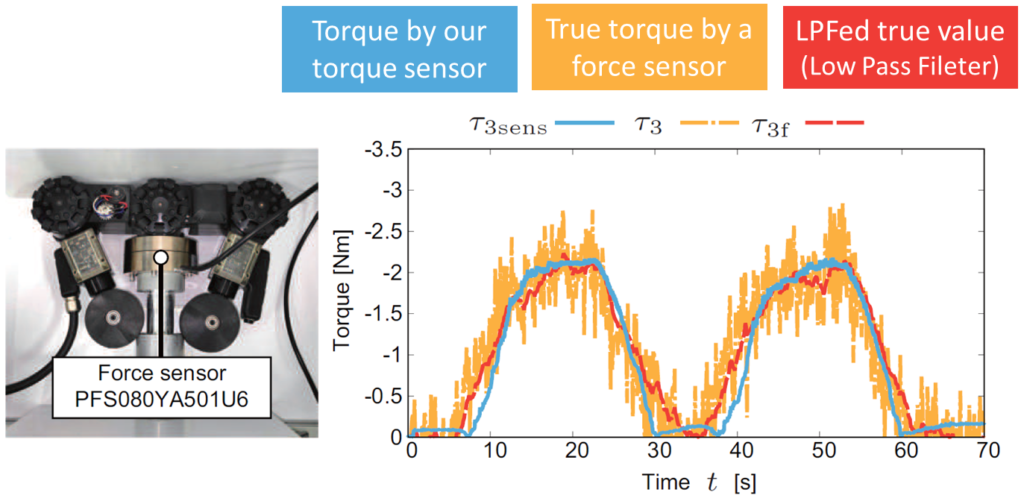
After several modifications, AIRo-5.2 was able to smoothly travel through more than 15 bends and 10 types of T-branch pipes with different gravity directions, and to generate more than 25 kgf (approx. 250 N) of traction force. In the experiment, the robot successfully traveled approximately 27 meters through a pipe course containing a total of 19 horizontal and vertical bends with an inside diameter of 4 inches (approximately 100 mm). No other robot in the world has been able to travel this deep through a pipe with such a winding path.
The results of these basic studies have been transferred to several private companies for the purpose of inspecting plants, gas pipes, and drainage pipes, and have been highly evaluated. The results have also been commercialized as an educational toy “Mecha Mole,” and are popular among children at the monthly “Pipe Robocon” (robot competition) held at science museums nationwide.
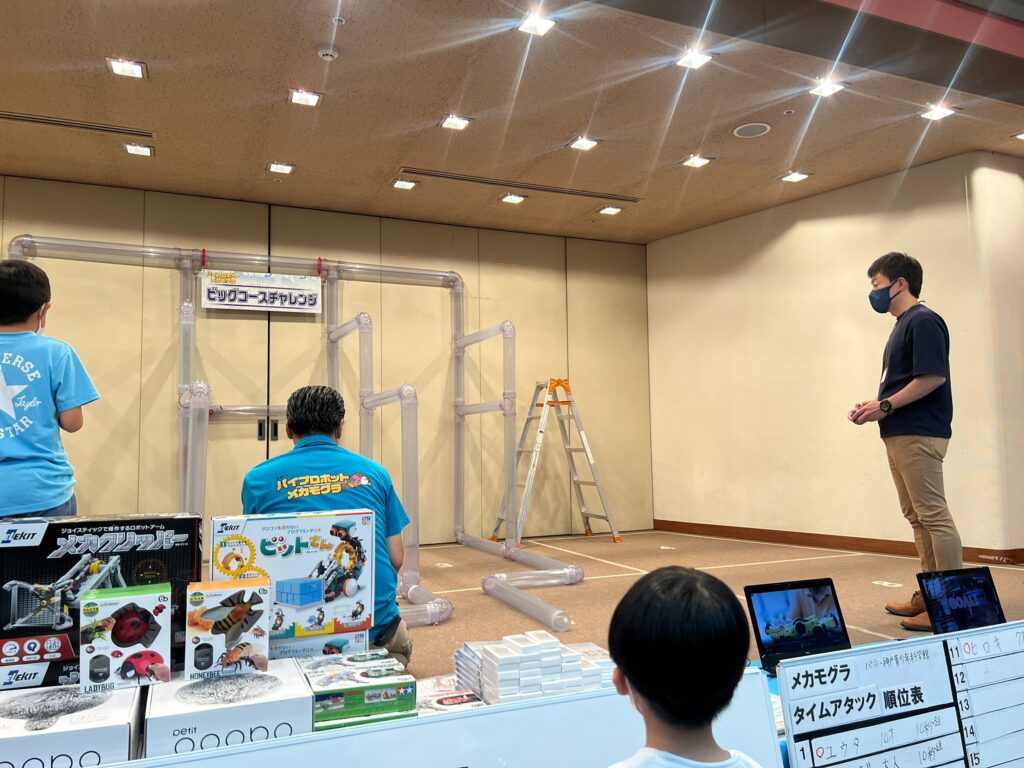
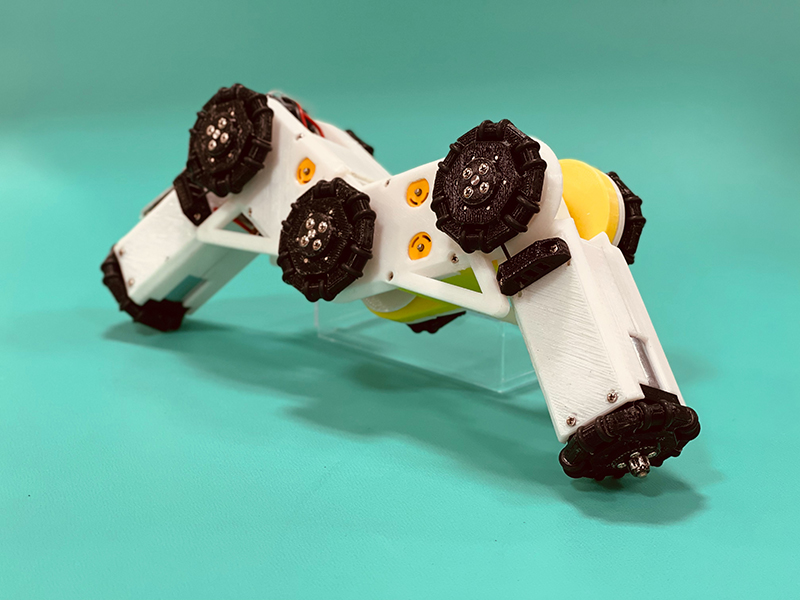
The name “AIRo” is derived from the initials of “Articulated wheeled In-pipe inspection Robot” and from the Japanese word “AIRo,” which means a narrow path.
Elemental studies related to this study
This result is the result of joint research with Ma-lab, Ritsumeikan University. The project was also supported by the Ministry of Land, Infrastructure, Transport and Tourism's Sewerage Technology Research and Development (GAIA Project) "Development of a Waterproof Snake-type Pipe Inspection Mobile Robot with Torque-sensing Active Joint Mechanism and SLAM Technology.
Related works
- Atsushi Kakogawa, Kenya Murata, and Shugen Ma, Automatic T-branch Travel of an Articulated Wheeled In-pipe Inspection Robot Using Joint Angle Response to Environmental Changes, IEEE Transactions on Industrial Electronics, Vo. 70, Iss. 7, pp. 7041-7050, 2023
- Atsushi Kakogawa, Kenya Murata, Shugen Ma, Vertical Bend and T-branch Travels of an Articulated Wheeled In-pipe Inspection Robot by Combining Its Joint Angle and Torque Controls, Proceedings of the IEEE/RSJ International Conference on Intelligent Robots and Systems (IROS 2022), pp. 13254-13259, 2022
- 村田憲哉,加古川篤,馬書根,1自由度能動関節のみを用いた連結車輪型管内移動ロボットのT字管走行 ―第2 報:角度センサの配置による関節角度およびトルクの計測性能の比較―,日本機械学会ロボティクス・メカトロニクス講演会 2022,2P1-M09,2022
- Atsushi Kakogawa, Yutaro Kushitani, and Shugen Ma, Automatic T-branch Travel of a Multi-link In-pipe Inspection Robot based on Joint Torque Value, 5th International Symposium on Swarm Behavior and Bio-Inspired Robotics (SWARM 2022), 2022
- Atsushi Kakogawa and Shugen Ma, A Multi-link In-pipe Inspection Robot Composed of Active and Passive Compliant Joints, Proceedings of the IEEE/RSJ International Conference on Intelligent Robots and Systems (IROS 2020), pp. 6472-6478, 2020
- 櫛谷侑太郎,加古川篤,馬書根,1自由度能動関節のみを用いた連結車輪型管内移動ロボットのT字管走行,日本機械学会ロボティクス・メカトロニクス講演会 2020,2P1-L08,2020
- 小川恭平,加古川篤,馬書根,川村貞夫,ロボット用せん断支持型高分子弾性要素の機械特性,日本機械学会ロボティクス・メカトロニクス講演会 2020,2P1-L07,2020
- Atsushi Kakogawa and Shugen Ma, An In-pipe Inspection Module with an Omnidirectional Bent-pipe Self-adaptation Mechanism using a Joint Torque Control, Proceedings of the IEEE/RSJ International Conference on Intelligent Robots and Systems (IROS 2019), pp. 4347-4352, 2019
- Atsushi Kakogawa and Shugen Ma, A Differential Elastic Joint for Multi-Linked Pipeline Inspection Robots, Proceedings of the IEEE/RSJ International Conference on Intelligent Robots and Systems (IROS 2018), pp. 949-954, 2018
Previous studies that served as references for this study
- G. C. Vradis and W. Leary, Development of an Inspection Platform and a Suite of Sensors for Assessing Corrosion a Mechanical Damage on Unpiggable Transmission Mains, Technical Report of NGA and Foster-Miller, 2004
- E. Dertien, S. Stramigioli, and K. Pulles, Development of an Inspection Robot for Small Diameter Gas Distribution Mains, in Proc. the IEEE Int. Conf. Robotics and Automation, pp. 5044-5049, 2011
- P. Debenest, M. Guarnieri, and S. Hirose, PipeTron Series – Robots for Pipe Inspection, in Proc. of the 3rd Int. Conf. Applied Robotics for the Power Industry, pp.1-6, 2014
- K. Tadakuma, Tetrahedral Mobile Robot with Novel Ball Shape Wheel, in Proc. the First IEEE/RAS-EMBS Int. Conf. Biomedical Robotics and Biomechatronics, pp. 946-952, 2006
- K. Tadakuma, R. Tadakuma, and J. Berengeres, Development of Holonomic Omnidirectional Vehicle with “Omni-Ball”: Spherical Wheels, in Proc. the IEEE/RSJ Int. Conf. Intelligent Robots and Systems, pp. 33-39, 2007
- D. Rollinson, S. Ford, B. Brown, and H. Choset, Design and Modeling of a Series Elastic Element for Snake Robots, in Proc. the ASME Dynamic Systems and Control Conference, pp. 1-5, 2013
- D. Rollinson, Y. Bilgen, B. Brown, F. Enner, S. Ford, C. Layton, J. Rembisz, M. Schwerin, A. Willig, P. Velagapudi and H. Choset, Design and Architecture of a Series Elastic Snake Robot, in Proc. the IEEE/RSJ Int. Conf. Intelligent Robots and Systems, pp. 4630-4636, 2014